SILICONE COMPRESSION MOLDING
The Benefits and Features of Silicone Material
Silicone is one of the most versatile and widely used materials across various industries. From personal care products and sports equipment to baby toys and pet products, silicone’s applications are nearly endless. But why is silicone so popular? Let’s take a look at the key reasons that make silicone a preferred choice for many businesses—and why you should consider using it too!
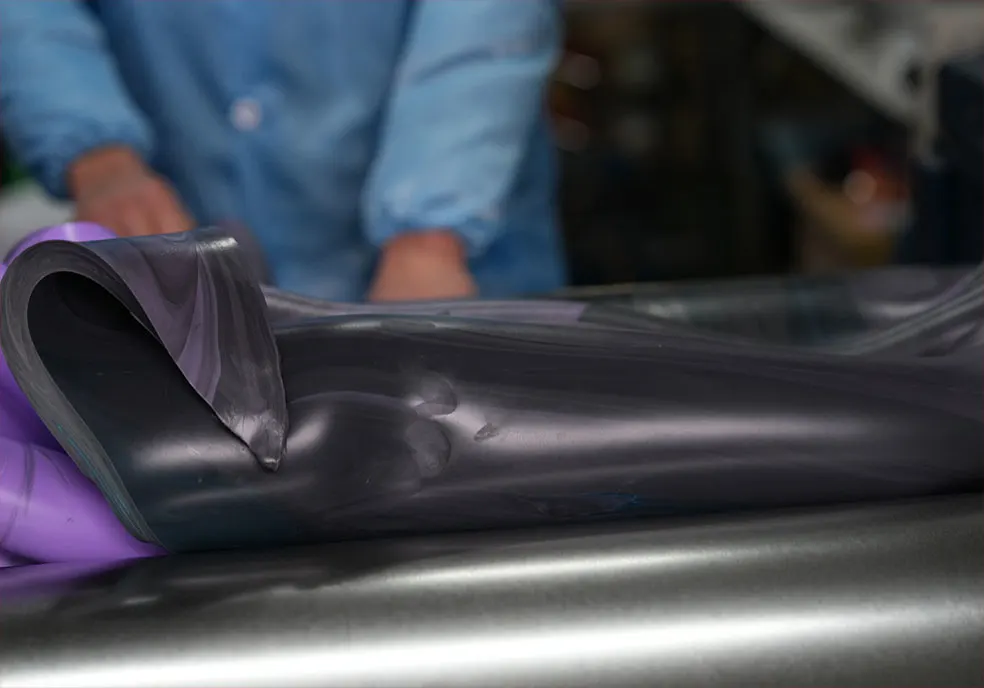
Safety
When produced correctly and sourced from reputable suppliers, silicone meets the necessary safety standards for a wide range of food-grade products. This makes it an ideal material for baby products, kitchenware, toys, and pet products, ensuring peace of mind for manufacturers and consumers alike.
Elastomeric Properties
Silicone’s rubber-like elasticity allows it to stretch, bend, and twist without losing its shape. This unique flexibility sets silicone apart from other materials that might crack, crumble, or break under similar conditions, making it highly durable for products requiring repeated use.
Durability
Known for its exceptional longevity, silicone retains its shape and performance even with regular wear and tear. It is tear-resistant, water-resistant, slip-resistant, and heat-resistant, making it perfect for products exposed to the elements or everyday handling.
Affordability
Silicone offers a cost-effective solution without compromising on quality. Compared to other materials, silicone is economical, allowing businesses of all sizes to produce high-quality products at scale without exceeding budget constraints. It’s the perfect balance of durability and affordability.
Silicone Compression Molding Processes
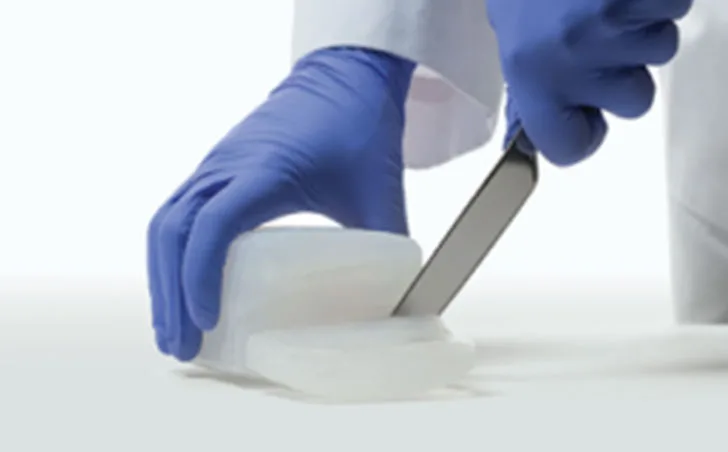
Step 1: Material Selection
The most suitable raw material is selected based on the product's intended use and customer requirements.
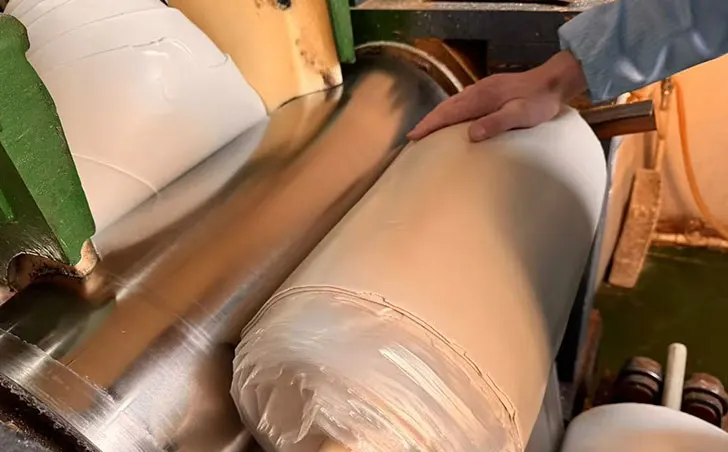
Step 2: Mixing Materials
Silicone raw materials are mixed according to the desired product hardness and color formulation to ensure consistency and quality.
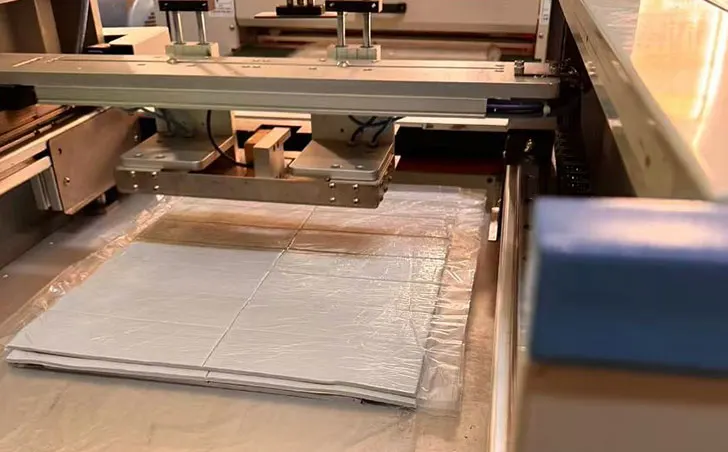
Step 3: Cutting Material
The mixed material is cut into strips or blocks, tailored to the specific specifications of the product.
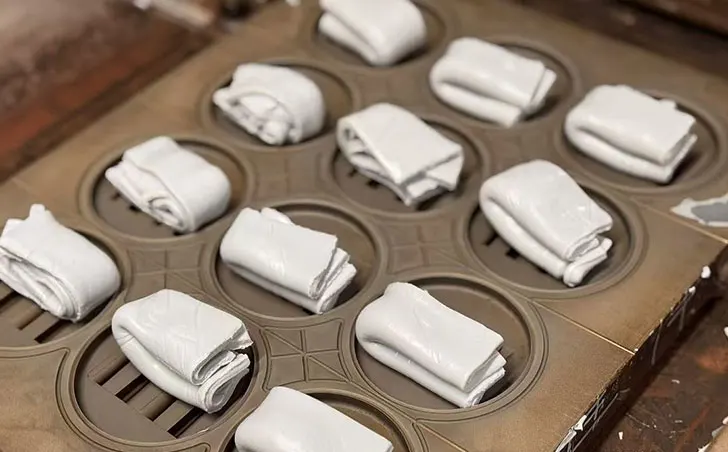
Step 4: Material Set-Up
The cut material is placed into the cavities of the mold. This process must be done quickly to prevent the mold temperature from dropping excessively.
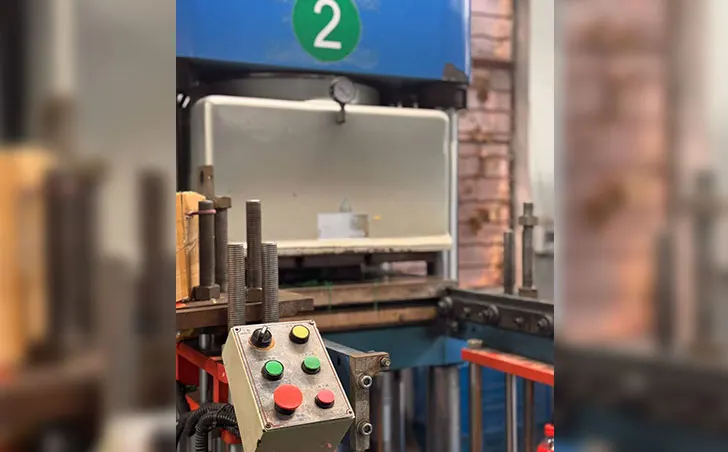
Step 5: Vulcanization
The mold is placed on the platform and undergoes vulcanization, where it is subjected to high temperature and pressure to form the desired shape and properties.
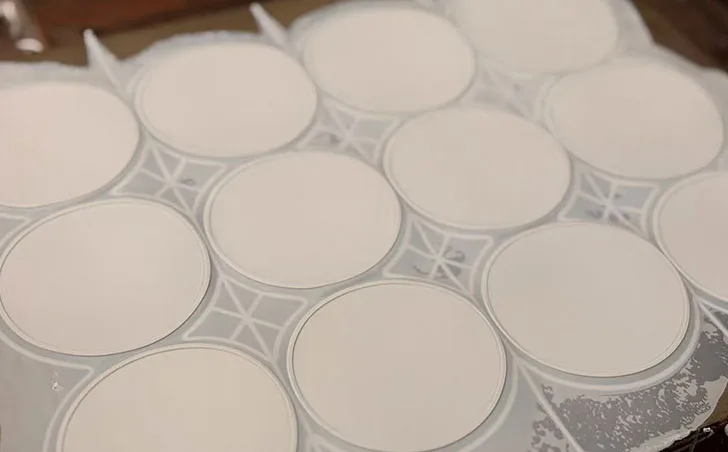
After the set vulcanization time is complete, the mold automatically opens, and the finished product is carefully removed.
The cut material is placed into the cavities of the mold. This process must be done quickly to prevent the mold temperature from dropping excessively.