OUR PROCESS
Silicone Product Manufacturing Process
The production of silicone products involves several processes. First, high-quality raw materials are precisely mixed, followed by shaping through methods such as injection molding or compression molding. Next, the products undergo high-temperature vulcanization to enhance their physical properties. After cooling, they are demolded and trimmed. Finally, the products undergo strict quality inspections to ensure they meet the standards before being packaged and shipped. Each step is carefully controlled to ensure quality.
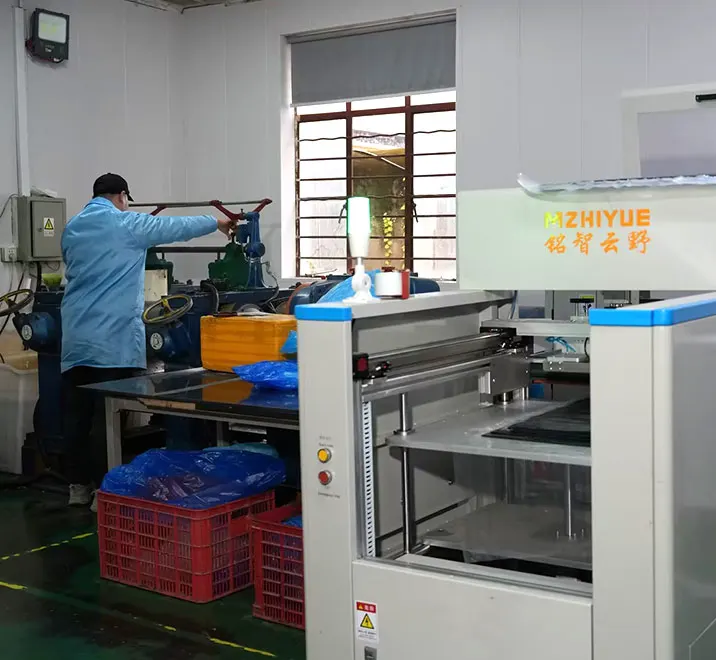
1. Compounding and Cutting
After the compounding process, the silicone compound undergoes further processing to ensure uniformity of the mixture, and it is then cut into appropriate sizes. These compounds can be customized according to the product's specific requirements, and they are cut or sliced to prepare them for the subsequent molding process.
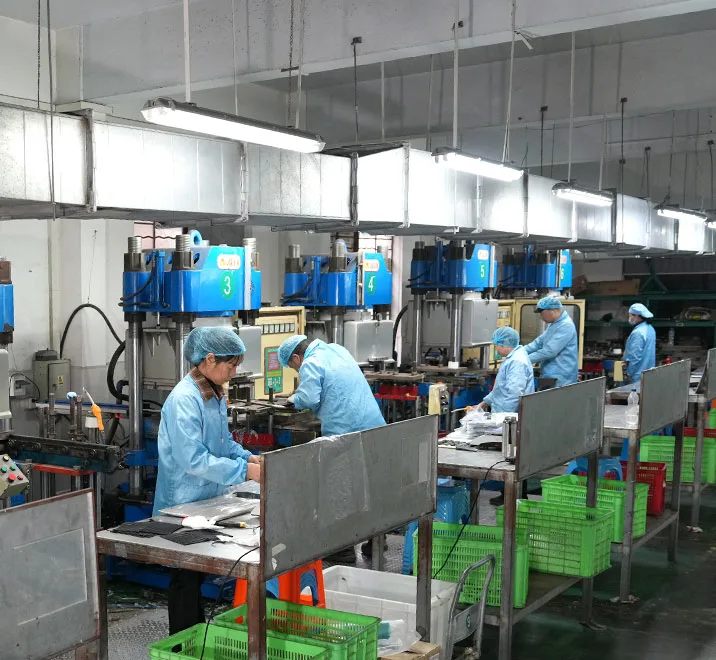
2. Compression Molding
Molding is the core step in silicone product formation. Compression molding machines or molds are used to apply heat and pressure to the silicone compound, allowing it to fill the mold and solidify into the desired shape. This process often involves high-temperature vulcanization to cure the silicone material, giving the product its final shape and strength. The precision of the molds and material selection are crucial to the quality of the finished product.
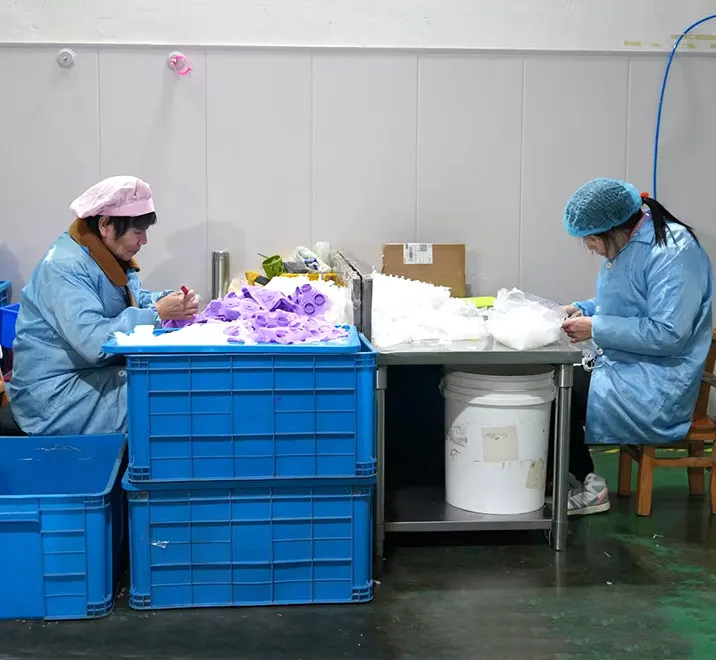
3. Trimming
After molding, excess silicone material, such as flash or overflows, may remain on the product. In the trimming process, these excess parts are removed manually or mechanically to ensure that the product has a clean, professional appearance and meets the required specifications. The trimming process must be done carefully to avoid affecting the product’s functionality or safety.
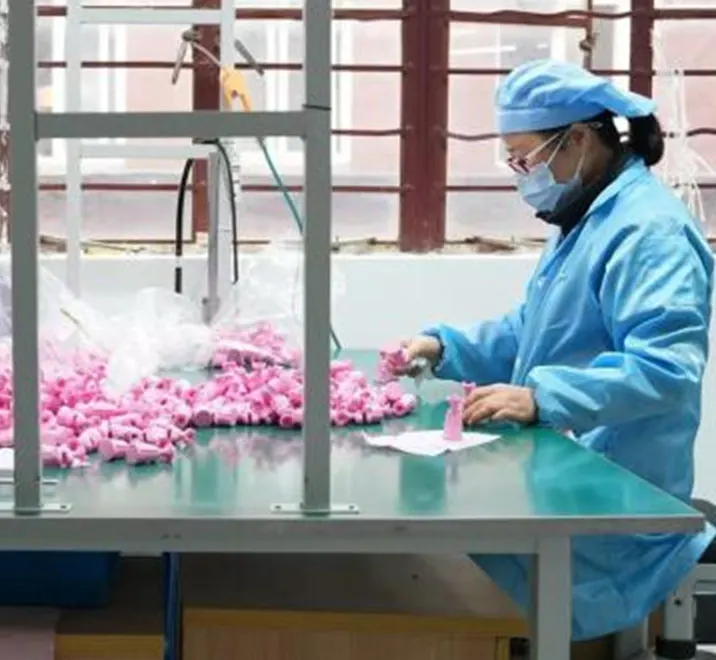
4. Inspection
The inspection stage is crucial to ensuring that every batch of products meets the required quality standards. This includes visual inspections (checking for defects like bubbles or cracks), dimensional measurements (ensuring the product conforms to design specifications), and physical property testing (such as hardness, tensile strength, etc.). Rigorous quality control during this stage ensures that the product meets both market and customer expectations.
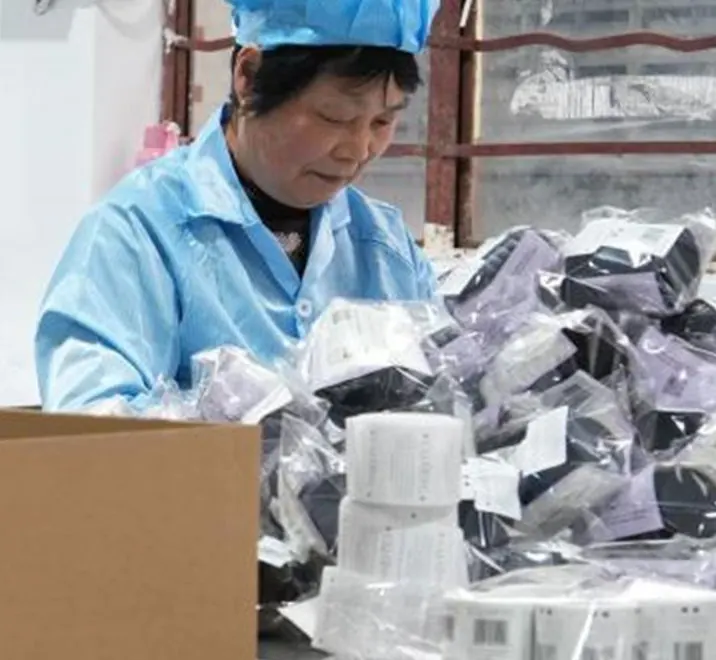
5. Packaging
Packaging serves both to protect the product and enhance its market appeal. Depending on the product, packaging may include plastic bags, cartons, or foam protection to prevent damage during transportation. Packaging must also meet environmental requirements, ensuring that materials are recyclable or compliant with relevant standards. The design of the packaging should consider factors such as storage, transportation, and display.
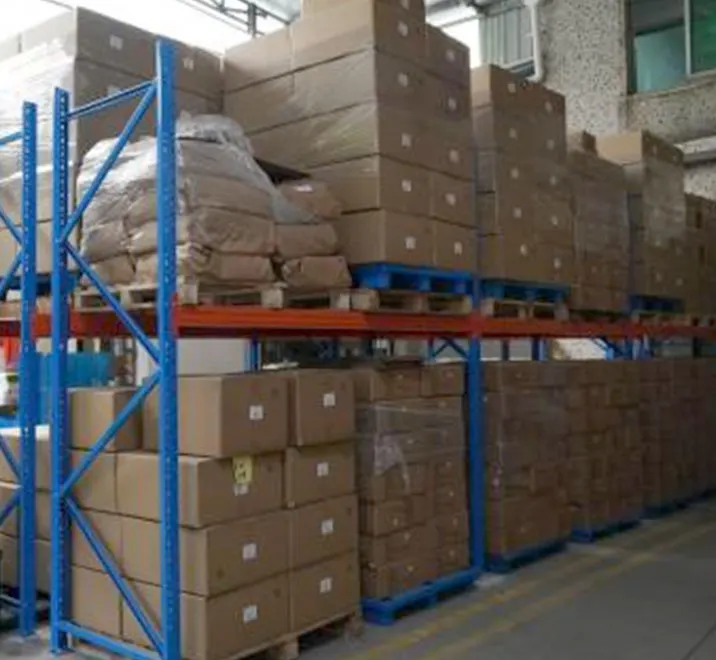
6. Delivery
Our factory is located near the Ningbo-Beilun port, one of the largest ports in the world, only 5km from the dock. Whether you choose LCL Ocean or full container sea way shipping , the shipping cost would be much more competitive. We have good cooperation relationship with the advanced express companies such as DHL ,UPS and FedEx, couriers could pick up goods each work day and goods normally be delivered in 7 days.
If you need customized silicon product manufacturing services, rely only on our professional-class process. Our team has the capacity and resources to bring your ideas to life!